Thermoplongeurs pour métaux légers
Chauffage par immersion ultra-compact en aluminium pour les fours de maintien de coulée sous pression
Pour assurer un contrôle précis de la température, ou pour effectuer une montée en température rapide de votre bain liquide de métal non ferreux, les thermoplongeurs Atherm représentent la technologie de chauffage par immersion la plus efficace parmi toutes les solutions existantes.
Grace au chauffage direct par immersion dans le métal, délivrant la puissance juste nécessaire, vous minimisez les pertes d’énergie et évitez la détérioration et les pertes de métal dues à la surchauffe, aux oxydes, corrindon et autres crasses
Thus, you also save productive time, avoiding time consuming and tricky cleaning operation of resistances.
This technology is suitable for high pressure die casting, gravity die casting and low pressure die casting, and as well for degassing, filtration unit or transport ladle re-heating.
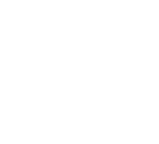
ENERGY SAVINGS
Atherm’s clients have reported 20%, 30% and even 40% energy savings using our immersion heaters in diverse settings.
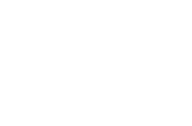
Decarbonization
As electrical devices, immersion heaters are a fully decarbonized heat source, generating no CO2 during the industrial process.
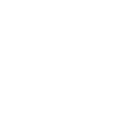
SAVE PRODUCTION TIME
Atherm’s clients regularly report high metal purity, exceptional quality of cast parts, and reduced metal oxidation.
ATHERM solutions to implement immersion heating for die casting
Depending your industrial organization and your project, we build with you a custom project to implement the relevant solution for you aluminium die casting workshop. Our technical offer is based on :
une gamme de thermoplongeurs ultra compacts
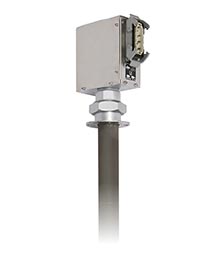
Fours de maintien avec thermoplongeurs
De 750 kgs à 2 tonnes, nous pouvons participer à la conception de fours dédiés à l’utilisation des thermoplongeurs afin d’assurer un maximum d’efficacité à l’installation en termes de performances, d’économies d’énergie, de productivité et de préservation de la qualité du métal.
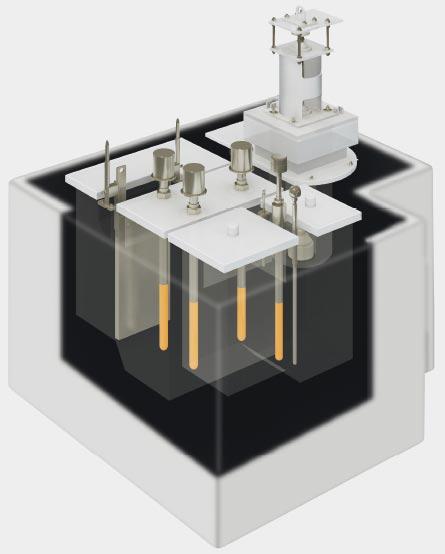
Atherm’s Supratherm Dual 75 : a unique 2-in-1 immersion heater also capable of preheating furnaces
In January 2024, Atherm officially launched its brand-new product: Supratherm Dual 75
What is the principle of immersion heating of aluminium and zinc alloys
Les fondamentaux de la technologie des thermoplongeurs ATHERM
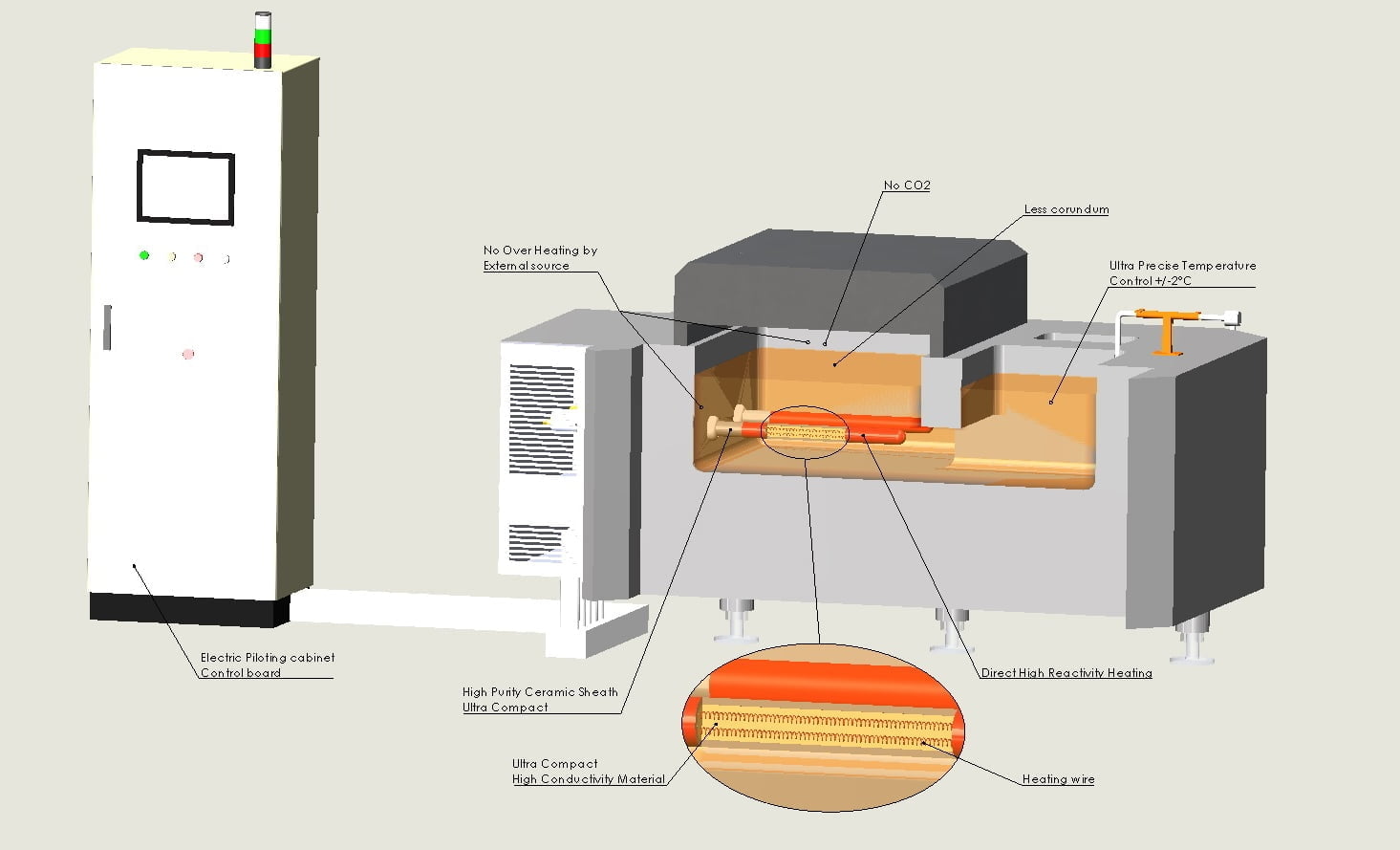
SUPRATHERM 28
8kW to 30kW

SUPRATHERM 32
8kW to 44kW
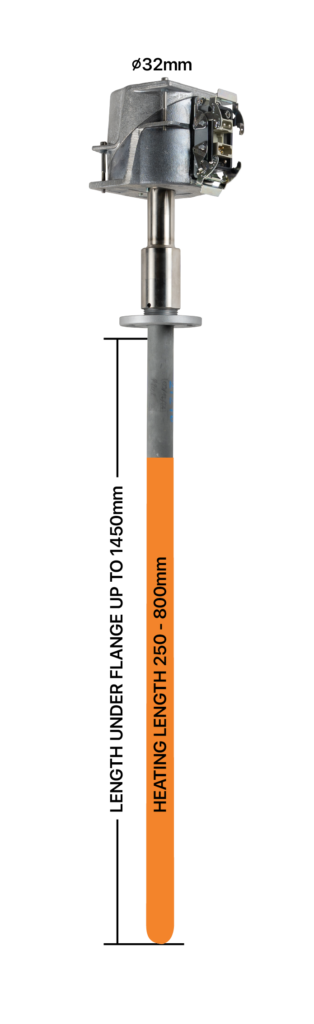
SUPRATHERM 40
12kW to 50kW

SUPRATHERM 55
10kW to 70kW

SUPRATHERM DUAL 75
2kW to 12kW in the air & 14kW to 27kW in the metal
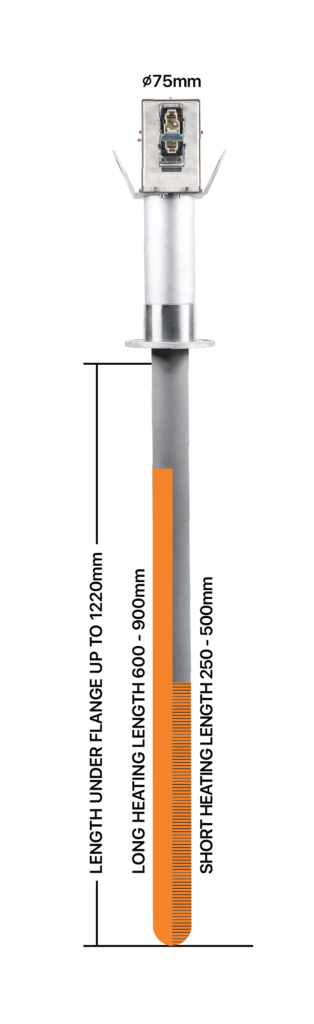
HEATING PIN
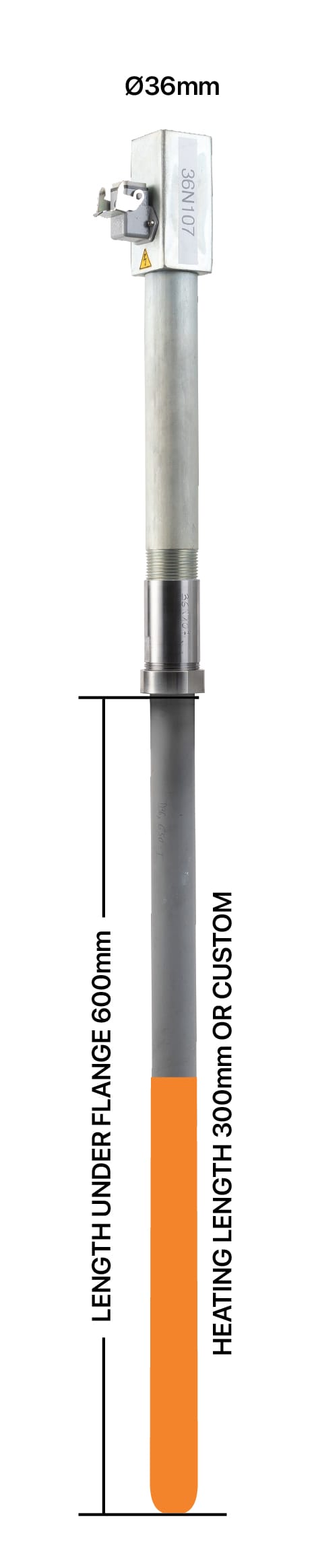
FURNACE FOR PINS PREHEATING
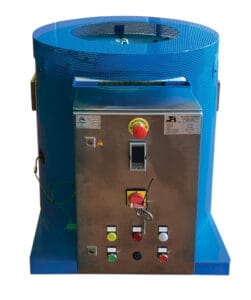
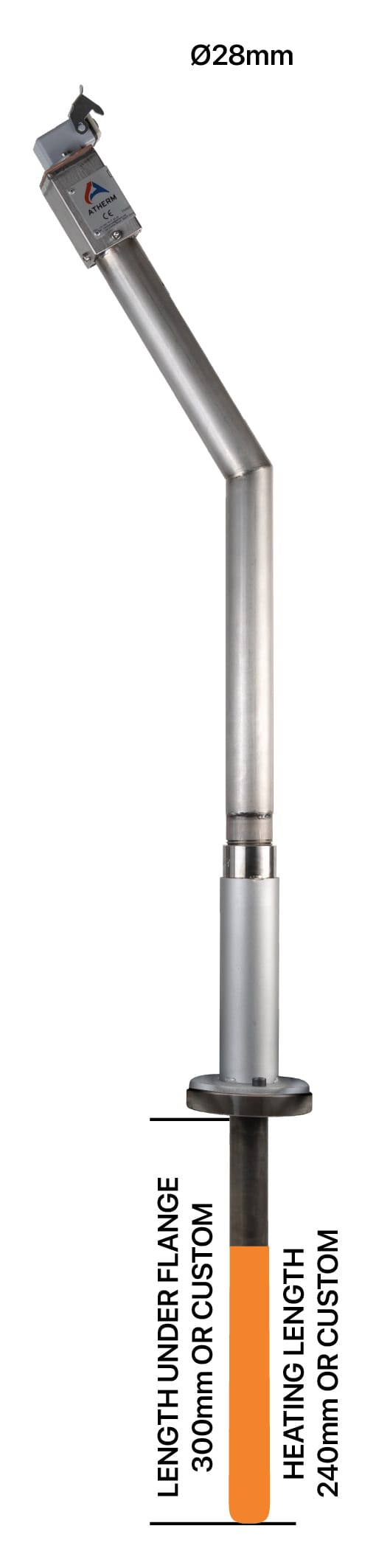
Mise en place des thermoplongeurs ATHERM
Conception de solutions de chauffage pour l’aluminium
Basée sur une gamme standard de thermoplongeurs, chaque solution est adaptée à votre application. Une équipe d’ingénieurs hautement qualifiés est à votre service.
Qualité « Made in France »
1000 thermoplongeurs par an
30 personnes à votre service
Une installation industrielle de 2000m2

Assistance technique et management de projets
Diagnostique de votre installation thermique Conception de l’implantation des thermoplongeurs Assistance à l’installation et formation sur site
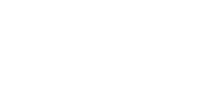
Short maintenance times
Targeted heating and precise temperature regulation help to optimize maintenance work. Cleaning depends on the quality of the metal and can even be unnecessary with high-quality baths. Atherm’s
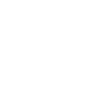
QUICK REHEATING
The light metal industry generally needs bath temperatures to rise rapidly. Atherm’s range of conductive immersion heaters was designed to generate very high surface power densities, enabling our technology to transfer very high power levels to the baths, for rapid reheating after maintenance or refilling.
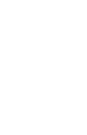
PREHEATING
The new Supratherm Dual immersion heater line offers an additional advantage of heating the air (when using the long heating unit), as well as the metal (with the short heating unit), enabling it to also be used to preheat the furnaces. This feature is also helpful when the level of the metal bath is too low since, when the heating unit is partially immersed and the power set appropriately, this heater is still able to work and heat.